Whenever I have the privilege of spending an afternoon at the cigar factory, the one detail that surprises people about my visits is that I usually do not smoke a cigar while I walk through it. At the heart of the factory, the urge to light up a cigar fades away. The reason for this phenomenon is because of the factory’s atmosphere. Inside, the air contains the perfume of aging tobacco leaves, telling the story of timeless Dominican craftsmanship. The torcedores’ impeccable skills never go unnoticed as they hand-roll cigars with precision and careful eye, inspecting each layered leaf. The rhythmic sound of cutting and wrapping the tobacco blends fills the space. It’s Caribbean artistry in motion that feels suspended in time, where tradition and heritage intertwine into a fine blend.
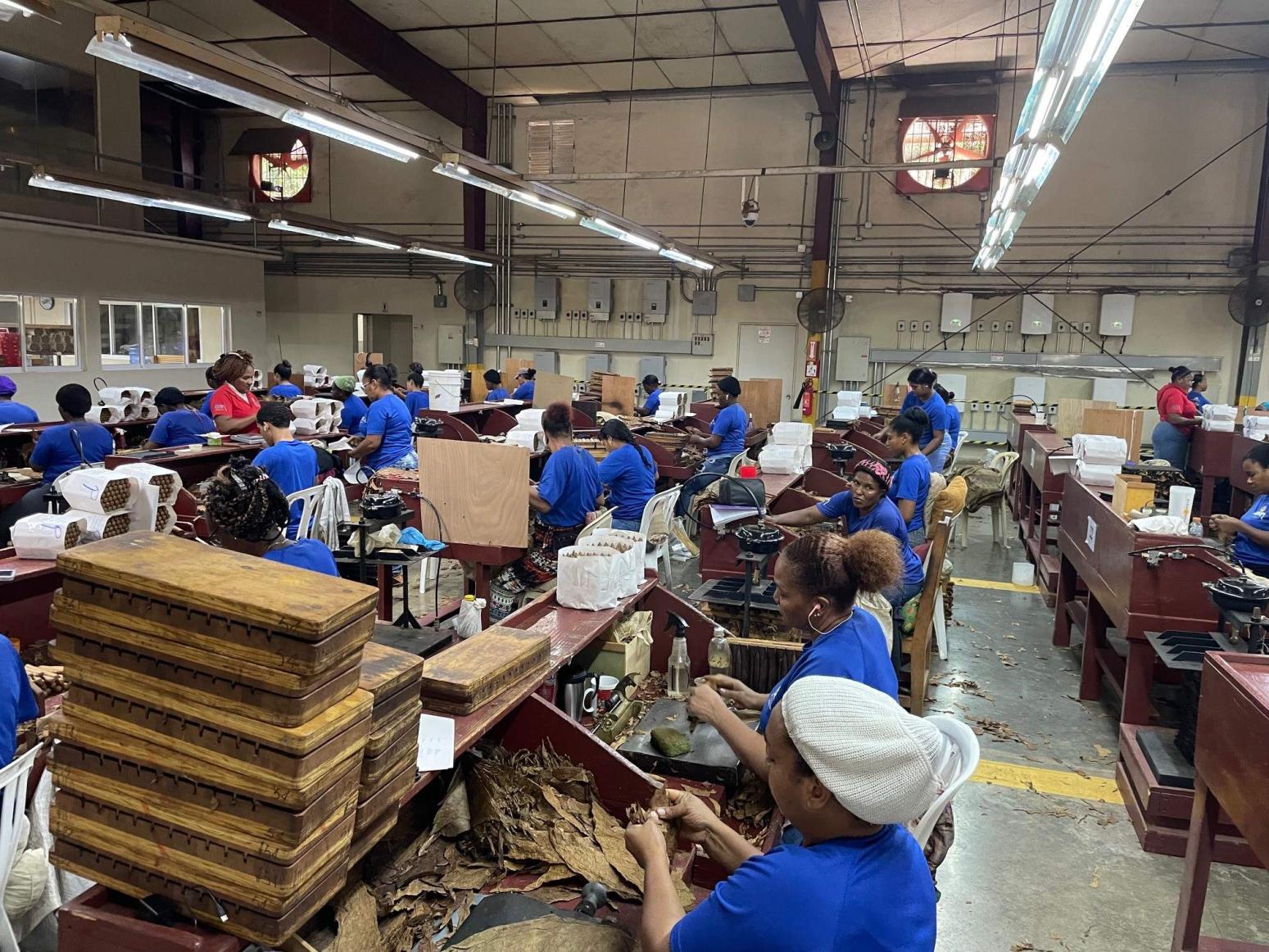
But before I get ahead of myself, the artistry begins long before the cigar is rolled. In fact, the journey of a handcrafted cigar starts with the process of aging which I like to call tobacco añejamiento. Tobacco añejamiento, or aging, is when the magic begins. In this stage, fresh fermented tobacco leaves undergo a meticulous transformation. This transformation removes the tobacco leaves' defects, softens their natural harshness, and allows their flavors to develop into something exceptional. It’s a process rooted in patience and precision, where time is the key ingredient.
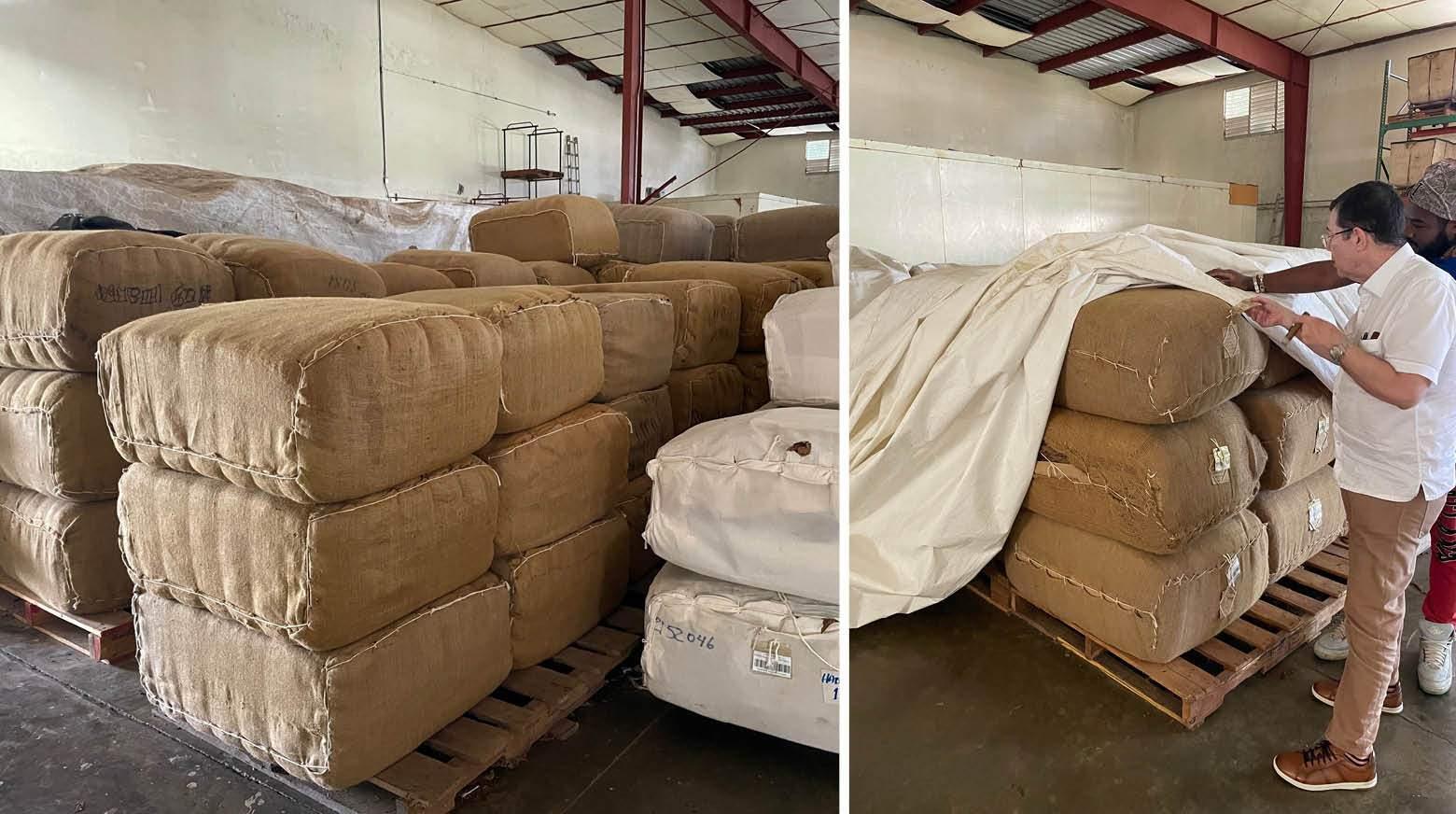
A day before the leaves get rolled into cigars, they must go through a re-humidification process called mojo. This step in the transformation of tobacco is essential for verifying that the leaves have the right texture and consistency for rolling. Mojo is crucial for the wrapper leaves, as it ensures they remain flexible and stretchable without tearing. During this process, the center stem is removed so each leaf half can be carefully applied to an individual cigar. It’s also worth noting that wrapper leaves undergo an additional sorting process to ensure that precise shades and sizes are produced.
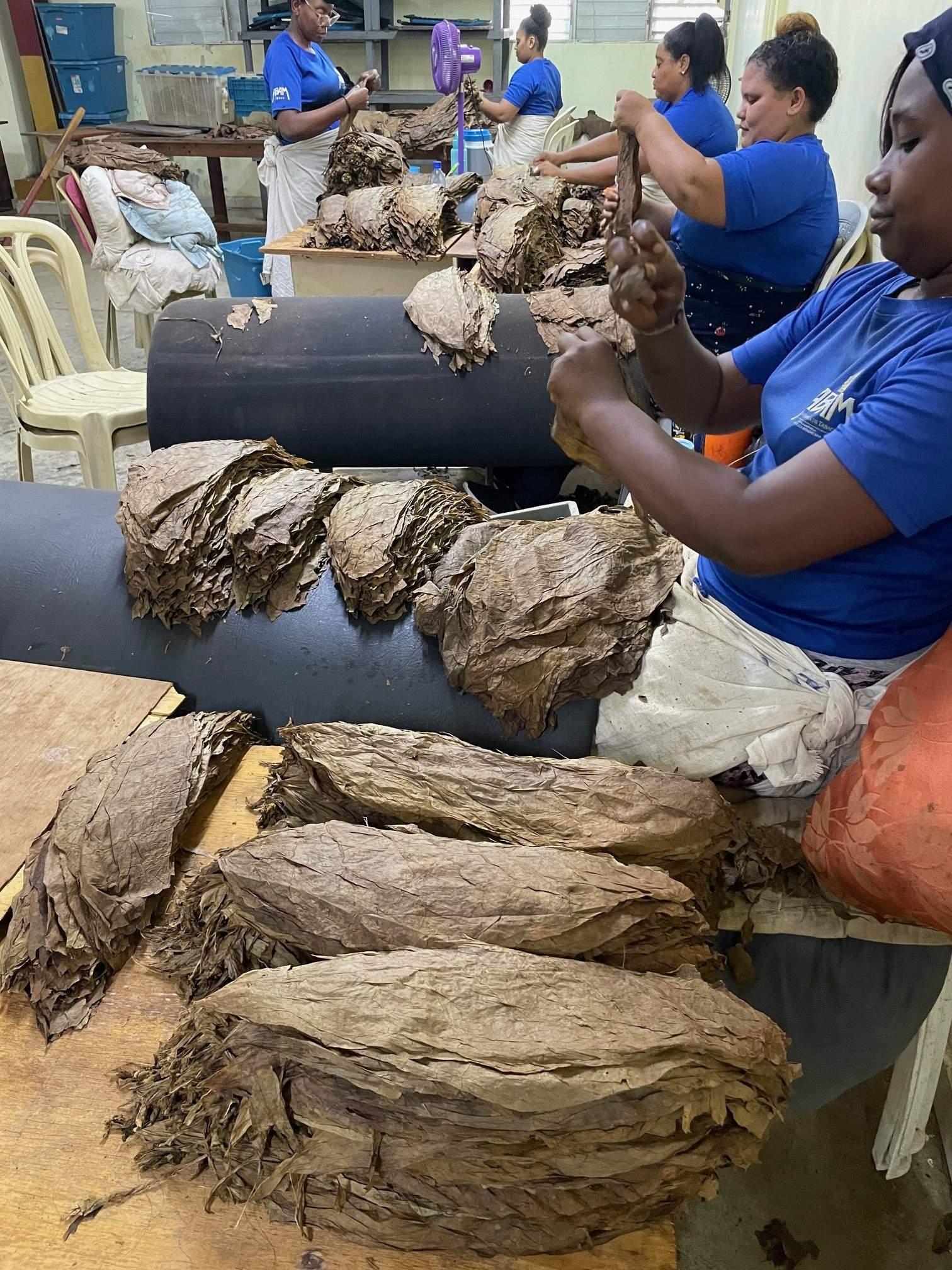
The next stage of the journey, known as blending, requires a master blender to distribute the “tobacco recipe” of a particular cigar to the rollers. This tobacco recipe includes precisely measured amounts of specific wrapper leaves, filler, and binder. Cigar rollers continue their artistry in motion by blending five filler leaves and wrapping them with a binder leaf. At this point, the cigar enters the bunching process, which requires extreme skill. This is a result of the necessity to create a perfectly balanced cigar that burns evenly and draws smoothly.
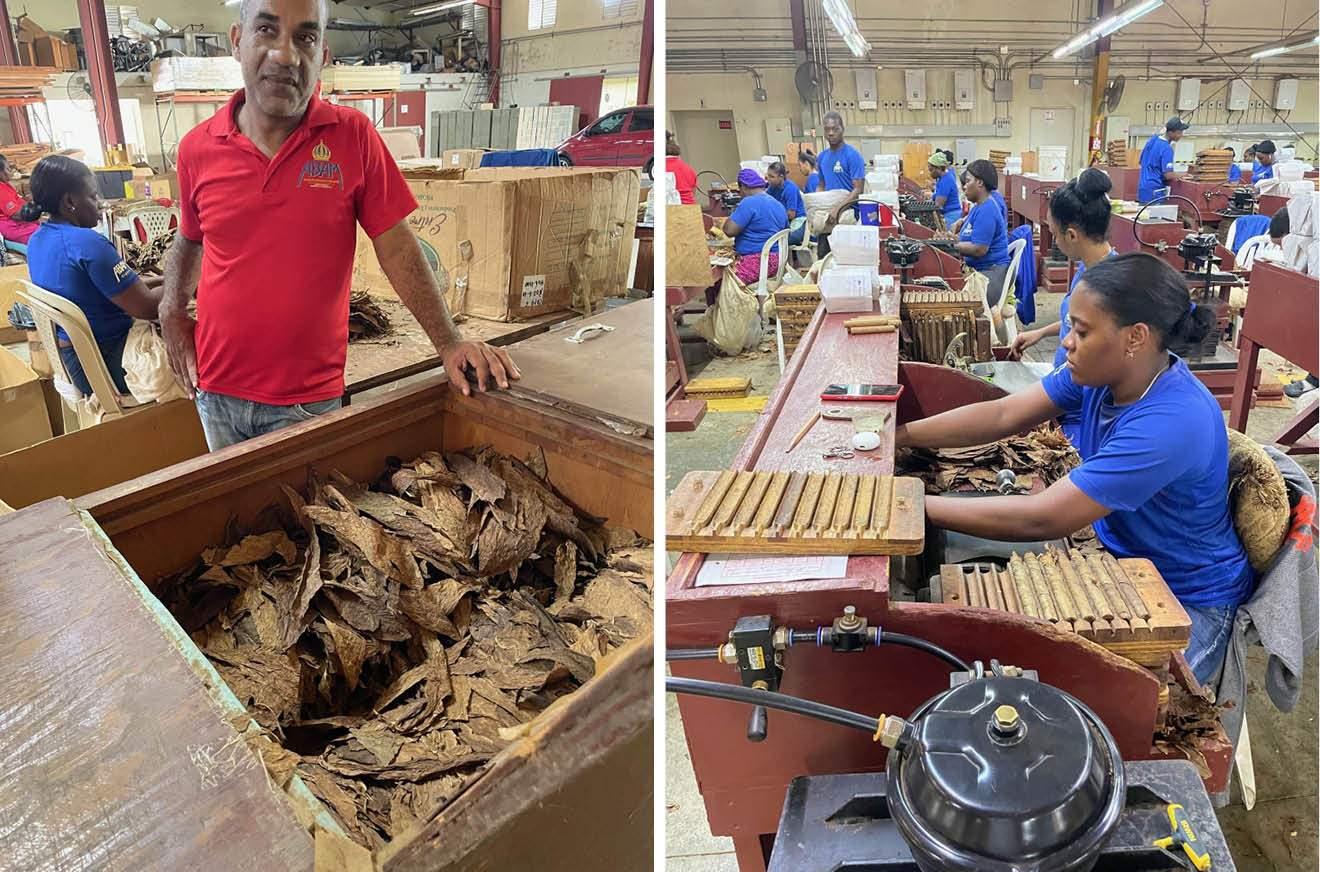
The bunch, or empuño, is placed in a cigar mold and press which rotates every 30 to 45 minutes to help the cigar achieve its proper shape. Additionally, the next phase of the cigar journey is the wrapping application to the empuño. First, half of a tobacco leaf must be trimmed with a chaveta to coat the cigar with ease. Our diligent torcedores will then stretch the wrapper leaf and wrap the empuño. Cigars are rolled in a rhythm reminiscent of a Juan Luis Guerra bachata, with movements flowing right-to-left and left-to-right depending on which side the wrapper leaf is used.
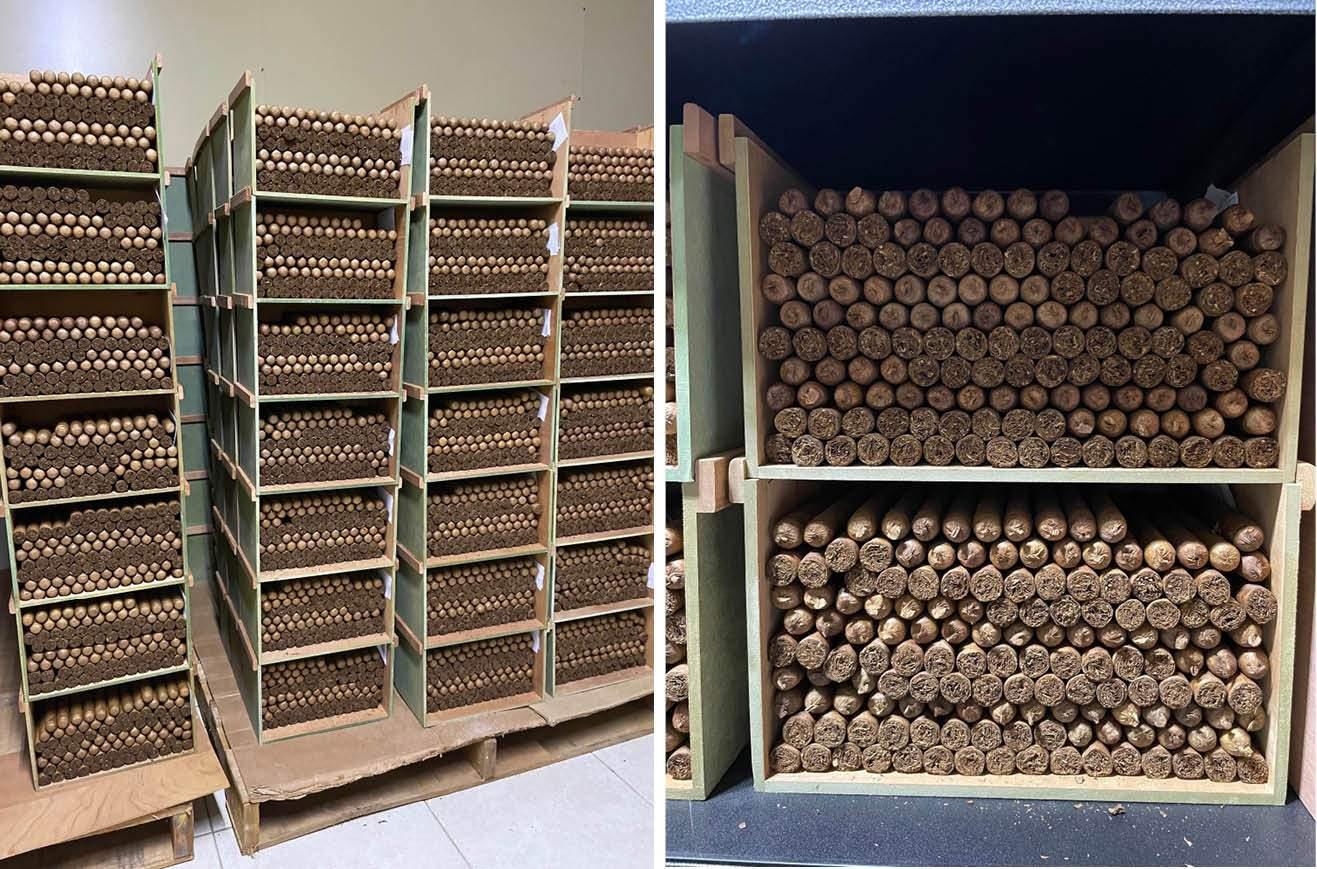
In the cigar-making journey, a bit of goma, a natural vegetable gum, will be added to the head of the cigar to ensure the cigar’s durability. On the cap, a round cut of the leaf is added to the top of the head as the ceremonial finish of the cigar. After the cigars are rolled, they will be measured, weighed, and smoked by a professional to ensure top Villiger quality control. Following this, the cigars will go through dehumidification for about a week. The handcrafted cigars will be released months or years later when they feel ready to continue their journey, reaching their peak in flavor and aroma. This aging process allows the cigars to develop their complexity and deepen their flavor profile. It’s in these quiet months of rest that the cigars undergo their final añejamiento, awaiting the perfect moment to complete their story when they are finally ready to be enjoyed.
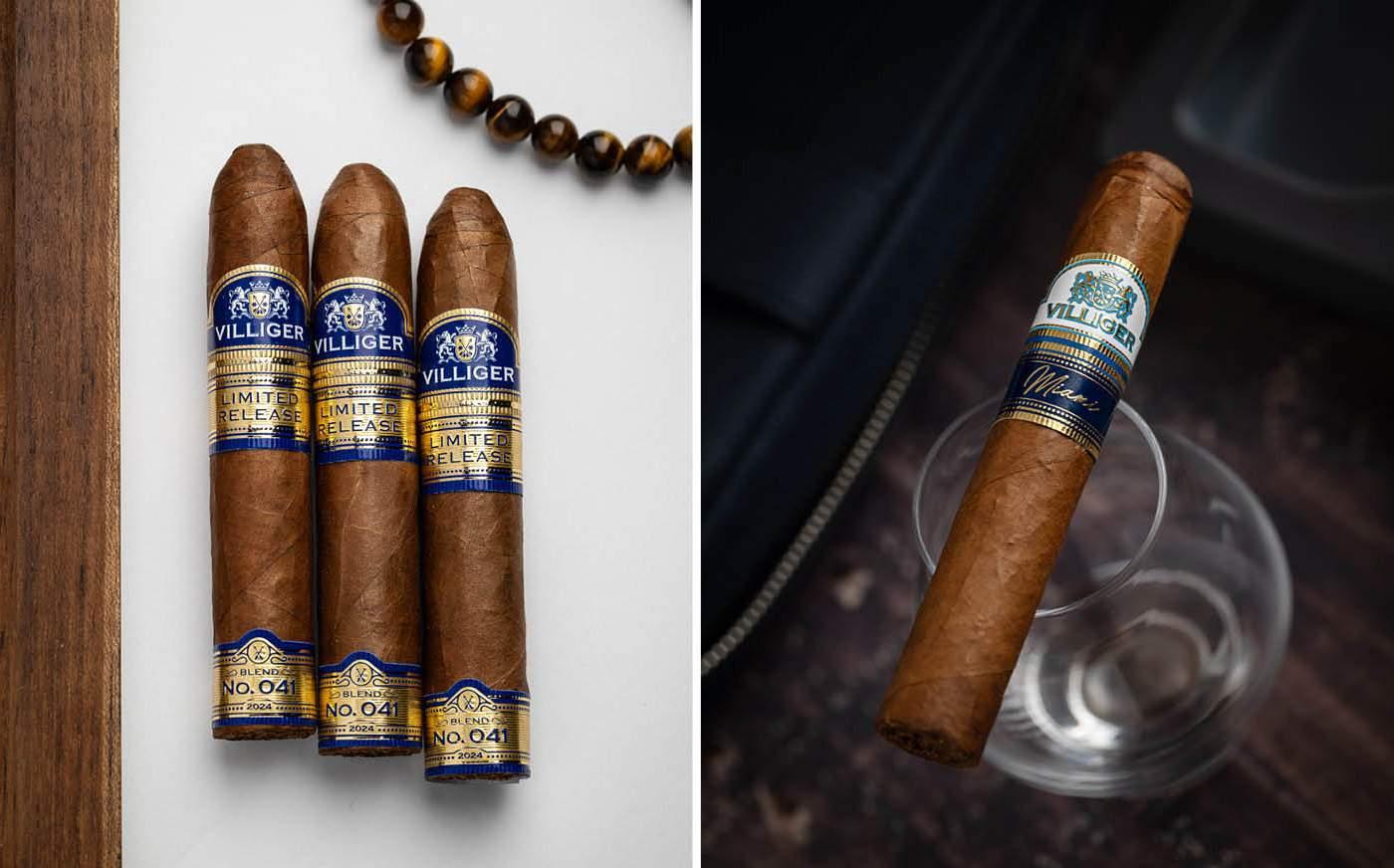